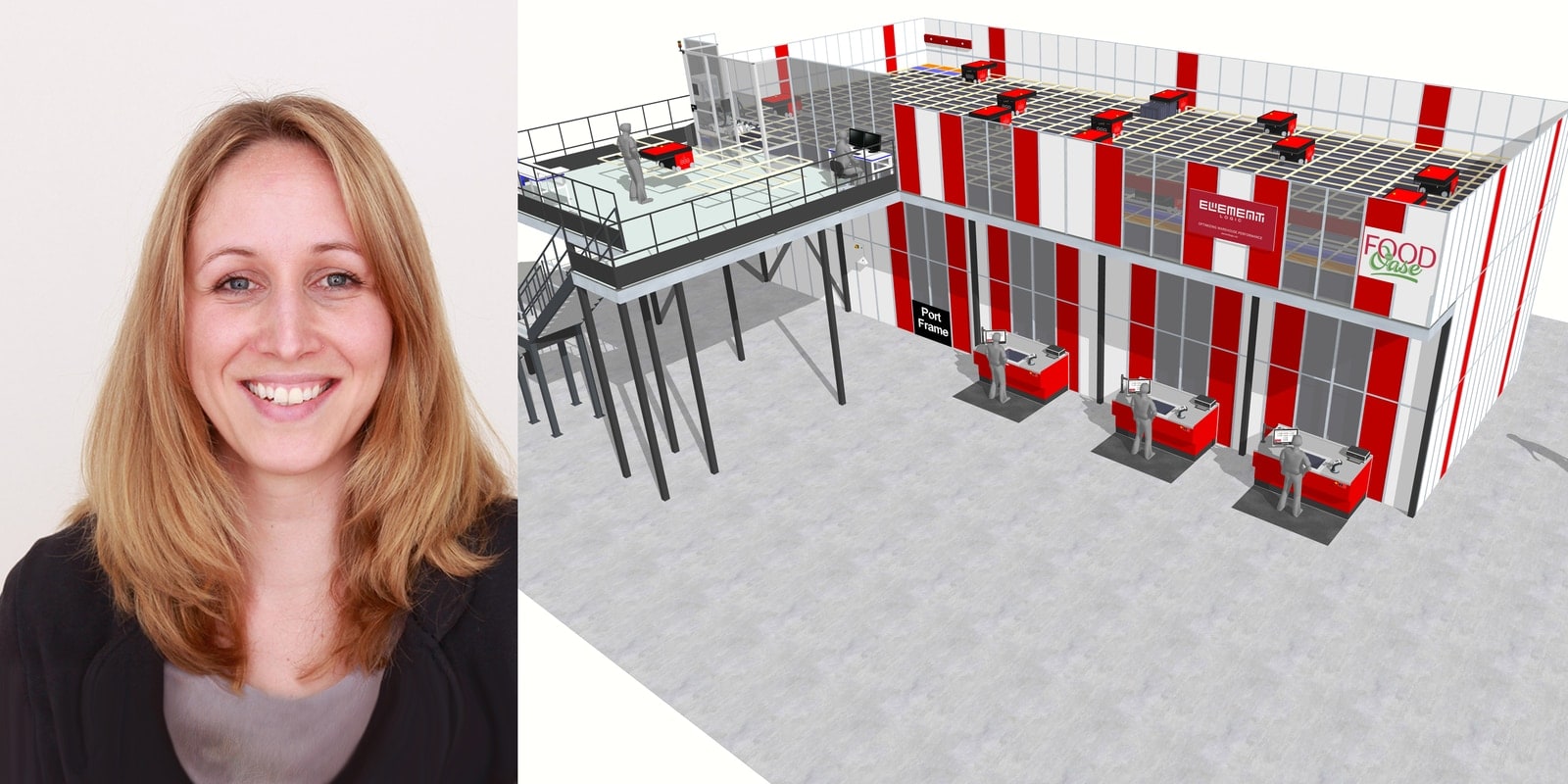
FoodOase offers food for people with allergies and intolerances. When the founder Sandra Neuber launched the web shop in 2007, she was one of the first in Germany to sell allergy and intolerance friendly food products online. Having started as a very small project in her own garage near Hamburg, FoodOase has over time grown to be the leading provider in the e-grocery segment. In 2019, FoodOase experienced further sales growth through the integration of the online shop querfood.de. In the first half of 2020, there was another significant increase in order volume, which was partly caused by the consequences of the worldwide pandemic, Covid-19.
In the past, FoodOase handled its warehouse logistics externally via a 3PL provider, who experienced the rapid growth of the company with its manually operated warehouse as an increasing challenge. Looking at the growth forecasts which will remain very positive, Sandra Neuber quickly realized that a new logistics concept was necessary. As a result, the entrepreneur rented a logistics hall in Geesthacht east of Hamburg and decided to take over the logistics by integrating it into her own company.
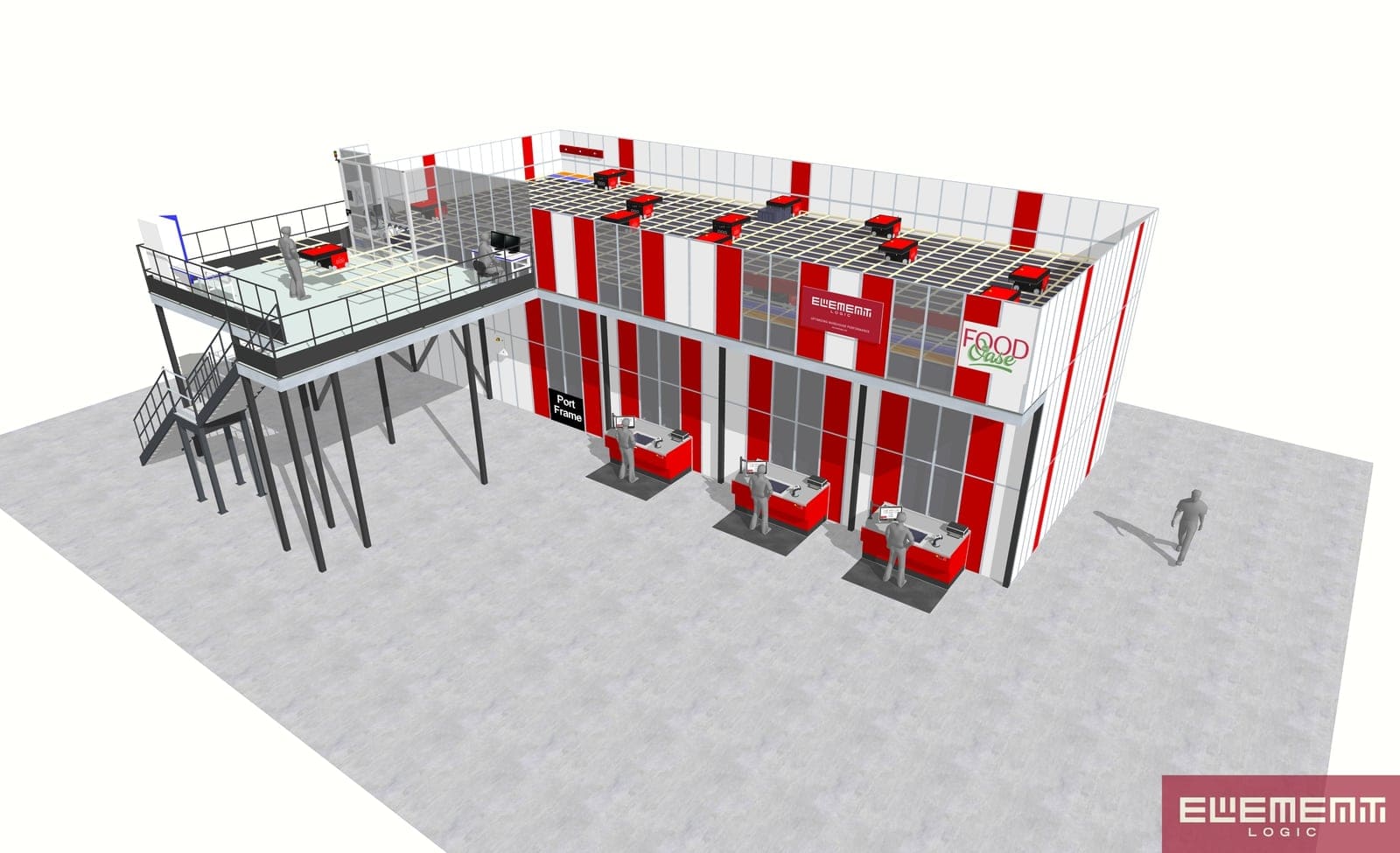
The planning and implementation of the new warehouse is conducted in cooperation with Element Logic and the German logistics consultant LogBer. The heart of the warehouse will be a fully automated, robot-based storage and retrieval system, AutoStore by Element Logic. In the first expansion phase, the system will have a size of 220 m² and is intended to process orders from the company’s online shops. According to the founder, this is one of the largest, but also most important investments in the history of FoodOase.
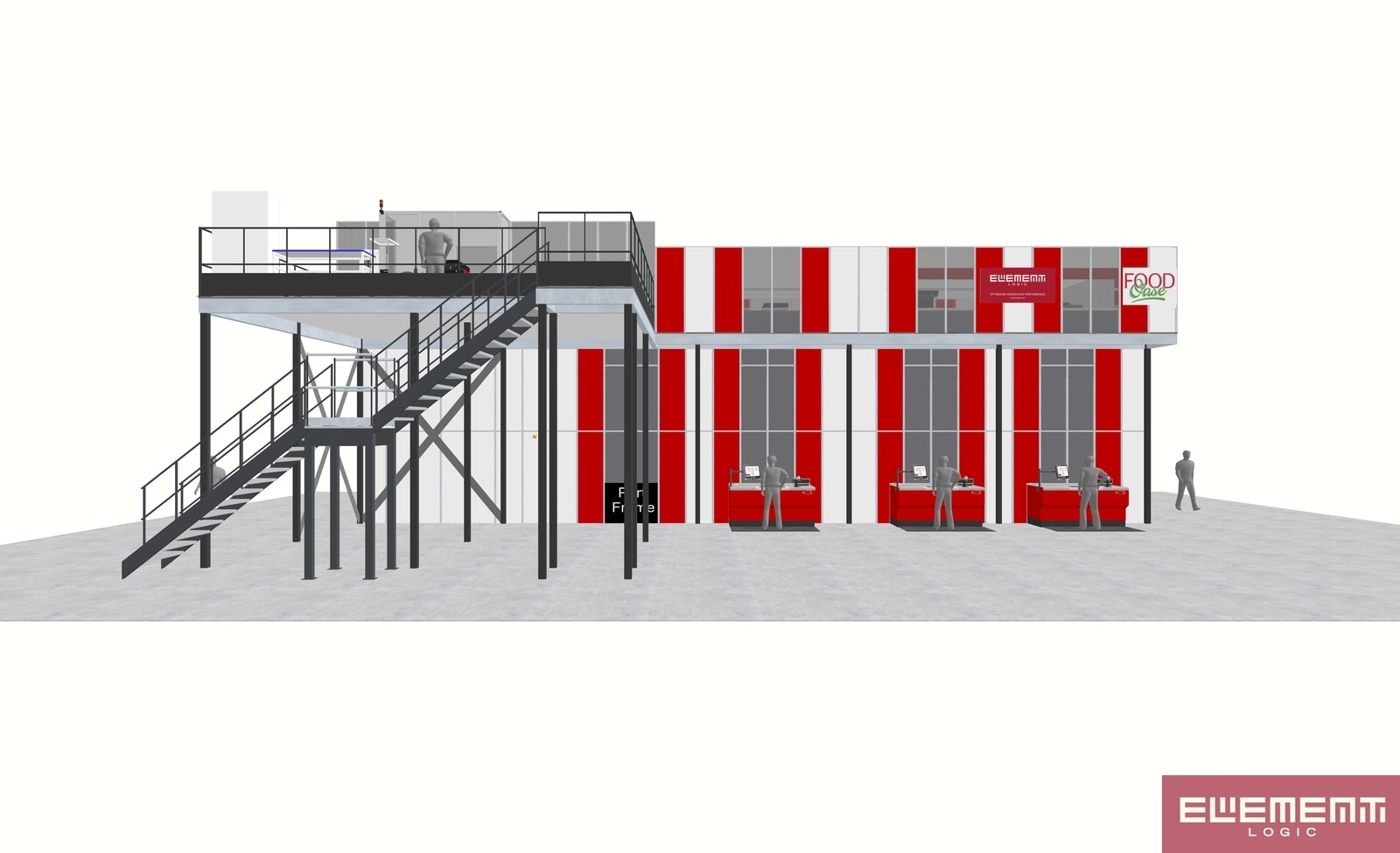
«Our customers expect us to ship their products very quickly and reliably. This is particularly important for them. Due to their special nutritional needs, they usually cannot find their daily food which they tolerate well in supermarkets. With our scalable, automated warehouse, we want to ensure that we will always continue to meet these expectations now and, in the future, says Sandra Neuber, CEO at FoodOase.
In addition to the AutoStore solution, Element Logic – in their role as general contractor – will also supply a warehouse management and material flow control system for this project. This system does not only manage and optimize AutoStore, but also the entire manual areas of the logistics center. In the first step, the AutoStore system at FoodOase will contain 6.100 storage bins and 13 AutoStore robots. Three carousel ports are available for goods in- and outbound. The finished installation is to be handed over to the customer by February 2021.